As a newcomer to the world of MIG welding, it's understandable to have questions about the correct set up for your welding gun. In particular, one common query is about the optimum distance for the contact tip to protrude from the nozzle on a Miller M-25 gun. In this blog, we'll delve into this topic and provide some tips for achieving the best welding results.
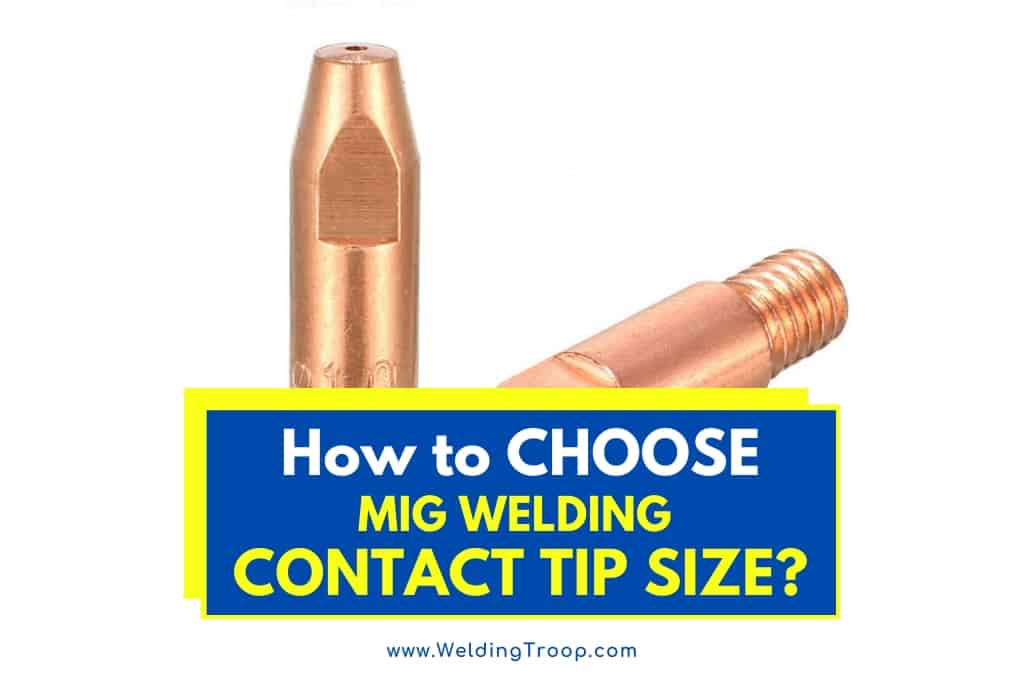
Firstly, let's take a closer look at the contact tip itself. This is a small, copper component that sits at the end of the welding gun, and it plays a crucial role in the welding process. The wire electrode which carries the welding current passes through the contact tip before exiting the nozzle and making contact with the workpiece. The contact tip is designed to have a precise opening, known as the orifice, which allows the wire to pass through while maintaining electrical contact.
So, how far should the contact tip be protruding from the nozzle? Well, there's no single answer to this question, as it depends on a variety of factors. Generally, however, it's recommended that the contact tip protrudes from the nozzle by around 1/4 inch. This allows for sufficient clearance between the wire and the nozzle, while also ensuring that the contact tip is close enough to the workpiece to create a stable arc.
It's worth noting that the distance between the contact tip and the workpiece can also affect the welding process. If the contact tip is too far away, the arc will be unstable and may even extinguish, leading to poor weld quality. On the other hand, if the contact tip is too close, the arc may become too concentrated, leading to burn-through or distortion of the workpiece.
To achieve the optimal distance between the contact tip and the workpiece, it's important to adjust the gun angle and travel speed. A 15-degree angle is generally recommended, as this allows for better visibility and access to the workpiece. The travel speed should also be adjusted to suit the thickness of the metal being welded, as well as the welding wire diameter and type.
Finally, it's worth taking care to select the correct contact tip size for your welding job. Different tasks will require different wire sizes, and the contact tip orifice should be matched accordingly. Using the correct contact tip size will help to ensure a stable arc, reduce spatter, and improve the overall quality of the weld.
In conclusion, while there is no hard and fast rule for the distance that the contact tip should protrude from the nozzle on a Miller M-25 gun, a distance of around 1/4 inch is generally recommended. Beyond this, it's important to adjust the gun angle and travel speed to ensure a stable arc, and to select the correct contact tip size for the job at hand. By following these guidelines, you'll be well on your way to producing high-quality MIG welds with your Miller welding gun.